he Bimotor Group supplied the Cgm Group with twenty “F36” Fpt Industrial engines intended to provide power for the construction of the Fehmarn Belt, the world’s longest underwater tunnel, between Denmark and Germany. These units were chosen for their operational reliability and emission levels compliant with the most stringent Stage V regulations.
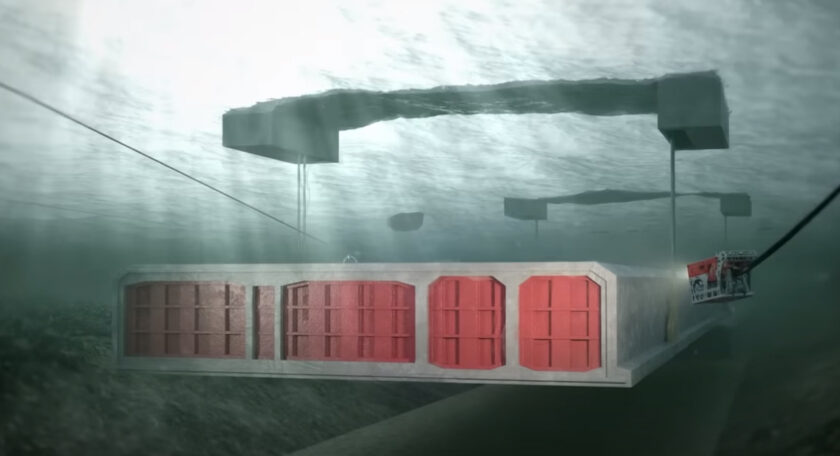
Fpt Industrial engines are supporting the generation of electrical power at the Fehmarn Belt construction site, located in the Baltic Strait between the German island of Femern and the Danish island of Lolland. By 2029, the two islands will be connected by the world’s longest underwater tunnel. This 18-kilometer tunnel will enable faster travel across the strait, thus enhancing connections between Scandinavia and Central Europe.
The Vicenza-based company Cgm, specializing in the design, manufacturing, and assembly of gensets for professional industrial applications, is actively contributing to the realization of this project. Their range of offerings spans from five to three thousand kilovolt-amperes, featuring generators equipped with power units from all major engine manufacturers. However, for this specific project, Fpt Industrial, facilitated by their distributor Bimotor, was chosen as the supplier of units to power the individual gensets. The “F36” series engines, with a displacement of three liters and 594 cubic centimeters, have been paired with generators capable of delivering up to 100 kilovolt-amperes of primary power, developed at 1800 revolutions per minute.
Performance and sustainability
There are three main technical reasons that led Cgm to choose Fpt Industrial’s “F36” engines as the only engines for such an important project. The first reason is performance level. The generators produced by Cgm will be tasked with supporting power generation during the laying and assembly operations of the tunnel segments on the seabed. This operation involves various tasks, resulting in highly variable loads in terms of power consumption.
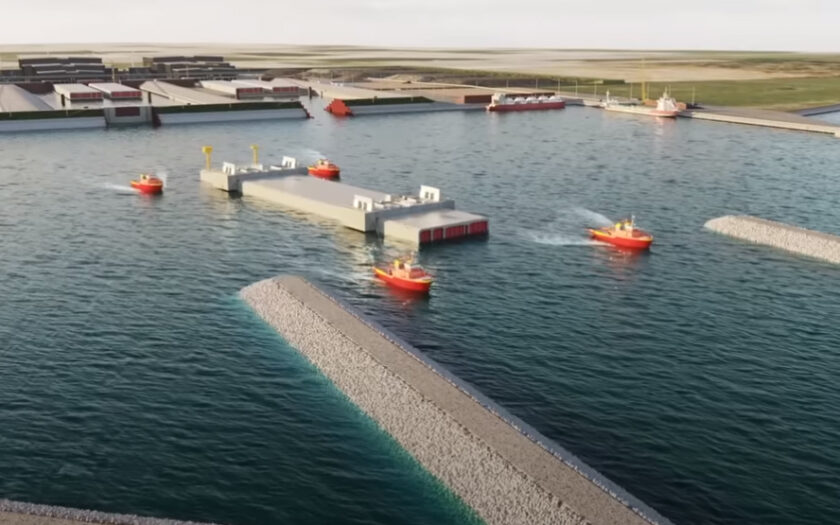
For this reason, Cgm has built four generators housed in as many containers, each containing five gensets operating in parallel. This architecture allows for generating up to two thousand kilovolt-amperes of total power, enabling each engine to operate when load conditions require it. Thus, each engine operates under maximum efficiency conditions, helping to minimize operating costs and the sustainability of the construction site. This latter need, considered fundamental by Cgm, has contributed to looking towards the “F36” engines.
Few engine manufacturers indeed offer, within the power generation segment, units compliant with the most stringent international emissions regulations. And none can boast Fpt Industrial’s “Hi-eScr2” exhaust gas aftertreatment systems. Pre-assembled and pre-validated groups that enable units to comply with stage V regulations. Facilitating engine integration into various operating contexts, whether stationary or on mobile machinery.
Maintenance every 600 hours
Another reason behind Cgm’s choice is the high reliability and ability to handle the required load. Even in challenging working conditions such as those at the Fehmarn Belt construction site. Notably, FPT Industrial has delivered the engines equipped with a cooling system specifically designed to withstand the thermal stresses to which the units are subjected on site. This solution, combined with the arrangement of engine accessories on a single side, the presence of hydraulic tappets, and filters designed to minimize maintenance interventions, allows the units to operate based on maintenance intervals scheduled every 600 hours of work.
Available in three power ranges, from 63 to 90 kilowatts, the “F36” engines stand out in the market for achieving operational performance without exceeding thermal and mechanical stress. This is due to a balanced design of the engine architecture. With the four in-line cylinders developing a displacement of three liters and 594 cubic centimeters, featuring cylinder liners with a bore of 102 millimeters and a stroke of 110 millimeters.
Fpt power for the Fehmarn Belt
The stroke-to-bore ratio of eight hundredths above unity stands out in its segment as the lowest parameter, thanks to the stroke of only 110 millimeters. This results in a piston mean speed of just over eight meters per second when calculated at the nominal speed of 2,200 rpm, while maintaining high combustion efficiency. The effective mean pressure, at the peak calibration of 105 kilowatts (143 horsepower), reaches 21 bar, thanks to the achievement of maximum torques in the range of 600 Newton-meters at 1,400 revolutions per minute.
The performance is also achieved thanks to the electronically controlled common rail fuel system operating at 1,800 bar and a single turbocharger for supercharging. All this comes in sizes and weights among the most compact in its category. The former are contained within just over three and a half cubic decimeters, with the cooling system including a fan and radiator slightly exceeding one meter in length and height, with a width below 700 millimeters. The weight of the unit without auxiliary systems stands at 320 kilograms, at the lower limit of its category. This weight, with the cooling system and auxiliary systems, does not exceed 4.5 metric tons.
73,000 tons per section
The construction of the Fehmarn Belt tunnel required the establishment of one of Europe’s largest construction sites and the construction of the world’s largest concrete element production site. Including a dedicated port. The 18-kilometer tunnel will be built from 89 prefabricated sections, each incorporating five adjacent conduits. Two are dedicated to road traffic and two to rail traffic, with a fifth serving as a utility conduit. The structure of each section, measuring 217 meters in length, consists of a steel frame embedded in concrete. A solution that brings the weight of each section to 73,000 tons.
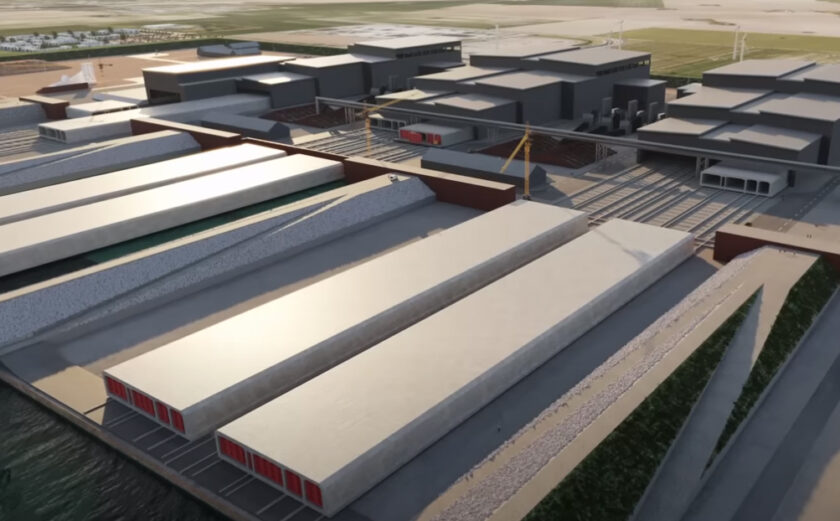
Production takes place in a dedicated factory organized into six production lines operating 24 hours a day, seven days a week. Allowing for the production of one section every nine weeks at full capacity. After leaving the factory, the sections are transported on a dedicated rail track to the purpose-built port, where they are positioned in a dry dock and sealed at both ends. Once the dock is flooded, the sections become buoyant, allowing them to be transported by sea to the installation point along a trench excavated on the seabed at a depth of 12 meters.
Opening in 2029
The elements are then sunk and positioned along the trench with a precision that allows for a margin of 15 millimeters over 15 kilometers in length. Once joined and sealed together, the sections are emptied to prepare for internal finishing works and installation of systems.
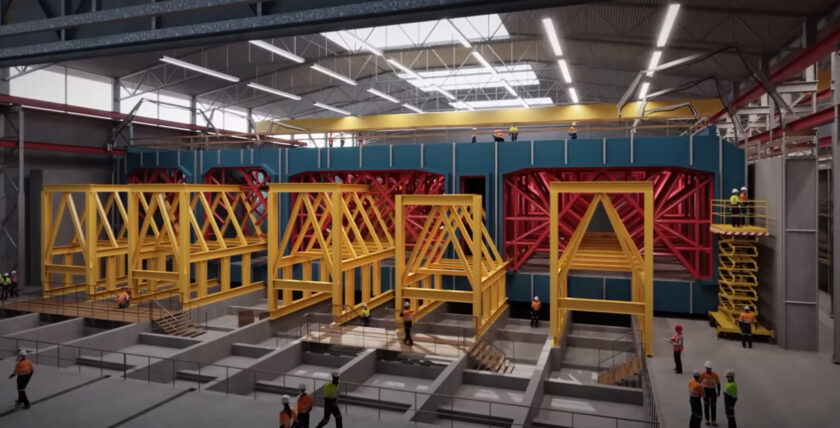
Once covered with soil and rocks, the trench will completely cover the tunnel elements, allowing for the restoration of the marine ecosystem. The 19 million cubic meters of soil, sand, and rocks removed to create the trench will instead be reused to create new beaches and lagoons alongside the tunnel entrance area, optimizing the environmental sustainability of the project. From 2029, trains and vehicles connecting the two islands will therefore see their respective routes reduced by up to 160 kilometers and will be able to reach their destinations in seven to ten minutes, depending on whether they are trains or rubber-tire vehicles.
Potenza Fpt per il Fehmarn Belt
Author: Jacopo Oldani
Translated by ChatGPT